Did you know that between 2015 and 2019, 70% to 80% of new molecular entities (NMEs) approved by the FDA were small molecules, and, in 2019, 68% of small molecules approved were oral dosage delivery?
Although drug delivery innovations in other areas may receive more excitement and coverage, for new drugs to be commercially successful, it is key that they are easy to manufacture, cost-effective and patient-friendly. For this reason, oral solid remains the most popular dosage form and continues to make up the largest segment of the global pharmaceutical market.
This demand has fueled innovative customizations and trends, forcing R&D scientists to use innovative ways to meet the growing needs.
Two examples of how market trends are inspiring new approaches to oral solid dosage forms are patient centricity and lean manufacturing. As patients have become more empowered in healthcare, patient-centric approaches to development are quickly becoming paramount to ensuring product success. Meanwhile, manufacturing simplicity has long been coveted to decrease manufacturing time and cost. While these emerging trends and novel approaches will undoubtedly bring added benefits to the industry. It is also no surprise that meeting new trends can often add difficulty to scaling and commercializing products.
Which leaves us with an important question, how can R&D scientists and formulation teams meet industry trends without creating manufacturing complexity? Read on to learn more about these market trends and find out how new excipient technologies are providing a solution.
Top Trend #1 – Patient Centricity
With greater access to information and increased awareness about drug safety, patients are becoming more informed about drugs. Consequently, pharmaceutical R&D has shifted in recent years to place patients at the center of both development and manufacturing decisions. To ensure patients are at the forefront of R&D, regulatory bodies have also become more focused on patient experience. For example, the FDA’s creation of PFDD (Patient-Focused Drug Development) ensures that patients’ needs, experiences, perspectives and priorities are being met.
In order to successfully provide products that meet this trend, R&D scientists are using high-quality excipient technologies, like Carbopol® polymers, to enable technical innovation. Here, these polymers can impart patient-centric features to new drugs in several ways, ensuring medicine is more convenient for consumers.
Meeting the Need for Patient Centricity – What’s the Frequency?
One way to improve patient centricity is to reduce the dosing frequency. Frequent dosing is not only inconvenient for consumers, but human error can also lead to doses being taken at the wrong time, reducing effectiveness. Standard immediate-release (IR) dosage forms cannot maintain plasma concentrations over prolonged periods. Therefore, the patient is required to take multiple daily dosages, leading to an increased risk of unwanted side effects caused by these high-peak blood concentrations after administration.
When modifying release formulations during drug product development, it is crucial to control the release rate of the active pharmaceutical ingredient (API). Hence, extended-release dosage forms provide an exciting solution for enabling formulations with reduced dosing frequency to benefit patients. Proven excipients, such as Carbopol polymers, tend to be the best facilitator for improving extended-release dosage forms and enabling successful control of the release rate of APIs.
Carbopol polymers have long been trusted by R&D scientists and manufacturers, as they offer a wide range of benefits for formulators. For example, Carbopol offers better control over dosage release compared to competitive materials, ensuring a slower drug release than other materials. As an excipient, Carbopol is more efficient than cellulosic materials (such as hypromellose, also known as HPMC), allowing formulators to effectively control release even at low usage levels.
Using Carbopol polymers alongside other excipients also has formulation benefits. When used in combination with other excipients, Carbopol:
- Lowers the total amount of excipient needed due to synergistic effects
- Provides flexibility in delivering target release profiles by varying ratios
- Lowers variability in the drug release profiles, particularly when using HPMC and Carbopol
Carbopol in Practice: Mucinex® Extended-Release Bi-Layer Tablets
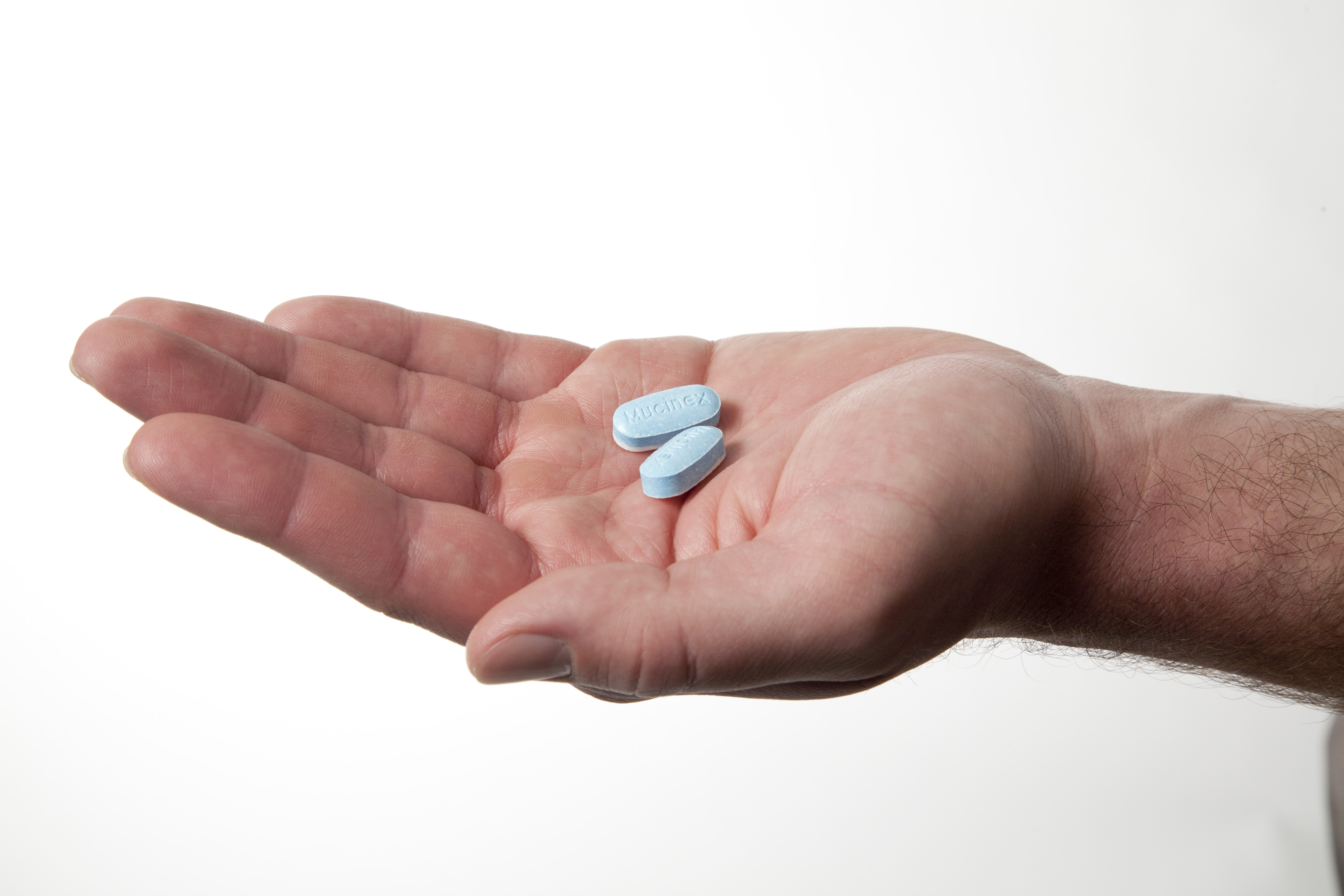
Carbopol has been used commercially across the industry to successfully improve controlled release. For example, when used by the well-known cold and flu medicine Mucinex, Carbopol enabled the generation of a unique bi-layer tablet and utilized the synergistic effects to effectively extend release.
Controlling drug release from Mucinex was especially challenging, as the active pharmaceutical ingredient, guaifenesin, is water soluble. However, Carbopol enabled both high drug loading and good control over release rate, even with a water-soluble API. This functionality resulted in a differentiated product that has gone on to achieve continued commercial success, including several product line extensions using Carbopol.
Meeting the Need for Patient Centricity – Do you have this in a smaller size?
Reducing the size of tablets is another trend to improve patient centricity. Large tablets are problematic for consumers. At best, they are uncomfortable to swallow and, at worse, can completely prevent consumers from taking the medication. For developers, reducing tablet size can improve the patient experience and increases the possible number of users. Innovative excipients can reduce tablet size during manufacturing and increase the patient centricity of the drug.
Carbopol in Practice: High-Dose, Extended-Release Metformin Tablets
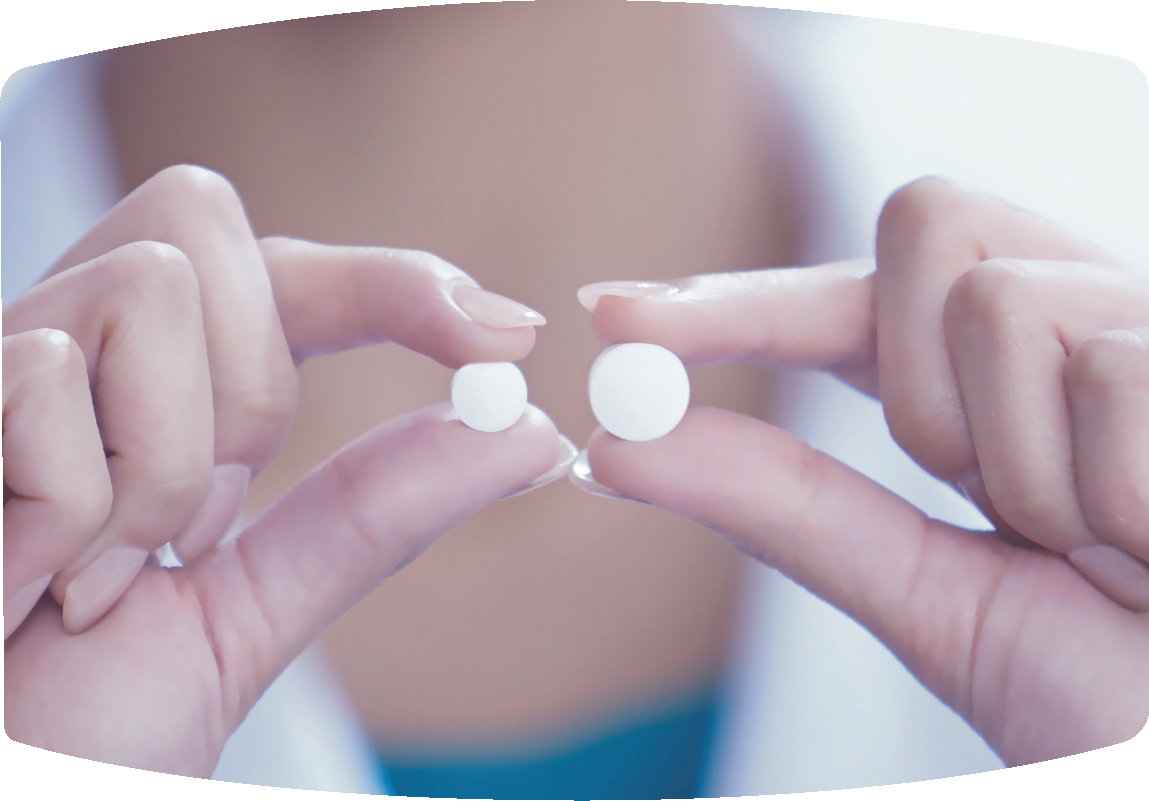
For example, commercial high-dose metformin tablets (drug range from 500-1000mg) suffer from large tablet sizes. Recognizing this challenge, Lubrizol developed metformin tablets using Carbopol to decrease the tablet size.
When Carbopol was used in metformin tablets, drug loading was improved from 62.5% to 80%, which led to reduced tablet sizes (22% smaller tablet size) than commercial products using HPMC. The Carbopol-based tablets also exhibited drug release within USP test IV specifications. In addition, Lubrizol filed a patent on the differentiated formulation, demonstrating the commercial value of incorporating Carbopol into formulations.
To learn more about Lubrizol’s work with improved metformin tablets, contact our team. Metformin is just one example of how Carbopol polymers enable differentiated, patent-protectable formulations that can offer both patient and commercial benefits.
Top Trend #2 – Lean Manufacturing
Lean manufacturing is another emerging global trend that’s impacting the development of oral solid dosage drugs. As a concept, lean manufacturing has been around for a while. However, in recent years, this trend has reemerged on the center stage as the pharmaceutical industry reevaluates its environmental impact and approach to sustainability.
Patient centricity and lean manufacturing are two examples of how market trends are inspiring new approaches to oral solid dosage forms. As patients have become more empowered in healthcare, patient-centric approaches to development are quickly becoming paramount to ensuring product successful. Meanwhile, manufacturing simplicity has long been coveted to decrease manufacturing time and cost. While these emerging trends and novel approaches will undoubtedly bring added benefits to the industry. It is also no surprise that meeting new trends can often add difficulty to scaling and commercializing products.
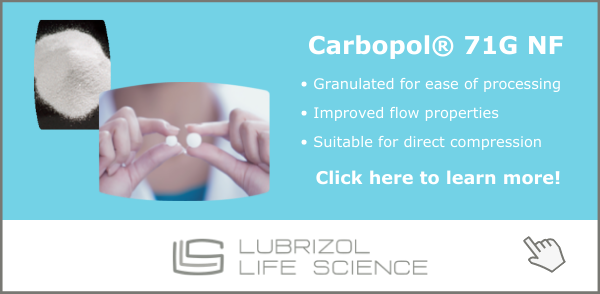
For developers working on processes for oral solid therapeutics, granulation is a key step that adds complexity. In this process, fine, non-compactable powders are turned into coarser agglomerates that can then be pressed into a tablet. It may sound easy, but granulation is complex and adds increased cost to the manufacturing process.
Using directly-compressible and pre-granulated excipients, such as Carbopol 71G, removes the granulation step and helps manufacturers to reduce the time and expense of these processes. This also provides additional benefits such as minimizing material waste and cost.
Want to learn more about the benefits of granulated Carbopol 71G?
Check out our webinar on “Enabling Oral Solid Innovation” here.
Outlook for Oral Solid Innovation
A shift toward increased patient centricity and lean manufacturing are key market trends that manufacturers need to meet. Extended-release and reduced tablet sizes are both important to improve patient centricity and drug success, while lean manufacturing is key to ensuring effective and efficient manufacturing. By leveraging innovative excipients, you can improve the quality of life for patients and increase the commercial viability of new products.
As experienced industry leaders, Lubrizol provides best-in-class technical support for our Carbopol polymers, including Carbopol 71G. Reach out to our team today to learn how Carbopol products can improve your oral solid dosage forms.