This custom 3D printed ESTANE® 3D TPU M95A suction cup was undamaged after 100,000 cycles of lifting and dropping a 0.5lb metal ball.
Forerunner 3D Printing Lives up to its Name in Multi Jet Fusion Printing
Operating out of its headquarters in western Michigan, Forerunner 3D Printing (F3DP) is proving to be an industry trailblazer in unlocking the full potential of the HP Multi Jet Fusion 4200 3D printer. Paul DeWys, the company’s founder, began his 3D printing endeavor in 2018 as a complement to his machine design business which serves a range of industries, with a special expertise in automotive applications. The company’s engineering chops and knowledge of real-world applications are responsible for the operation’s success in 3D printing, according to DeWys. “There are tricks to the trade, things you need to know,” explains DeWys. “Fully understanding these manufacturing machines and processes is critical to designing and printing parts that will actually do the job in that demanding environment.” Built upon its expertise and reputation in 3D CAD design, F3DP’s move into 3D printing was a natural progression and provided the company the unique opportunity to introduce its machine-design customers to the vast potential of additive manufacturing.
A cutting-edge TPU powder was the game-changer
When F3DP was introduced to Lubrizol's ESTANE® 3D TPU M95A, a whole new world of opportunities suddenly presented itself. After printing their very first pieces with this cutting-edge TPU, DeWys and his team were immediately struck by the rubber-like softness of the prints. Understanding what this could mean in delicate part assembly operations in which chrome-plated and painted parts must be protected from scratches, the F3DP team was eager to validate its performance for the company’s own machine build applications. “We have a lot riding on the parts that go out of here,” DeWys said, “so we really put ESTANE® 3D TPU M95A through the paces.”

As tough as it is soft
End-of-arm tooling manipulators in many automated manufacturing applications require a material that will not scratch painted or highly polished metal parts, such as automotive door handles. The repetitive nature of these processes, of course, means durability is just as important. To see just how much punishment ESTANE® 3D TPU M95A would endure, F3DP ran it through a gauntlet of tests, including relentless bending, compression and stretching, and even 10 hours of continuous sandblasting. ESTANE® 3D TPU M95A passed all their tests with flying colors. “Don’t be fooled by how soft it is,” explains DeWys. “This stuff wears like iron.”
Saves time in multiple ways
Right out of the gate, 3D printing eliminates the tooling and production time (as well as costs) of making similar parts with cast poured urethane. In contrast to the CPU process, which typically takes several weeks or more, F3DP can turn parts around in a matter of days. “And when you use CPU,” adds DeWys, “you better get it right the first time, because even small adjustments can mean another two to three weeks.” With 3D printing, making the same alterations can happen in a fraction of the time. What’s more, F3DP has found additional time savings using ESTANE® 3D TPU M95A when compared to other TPU materials. “The way this powder cleans up is jaw-dropping,” exclaims DeWys. “A little air and some light brushing and the unused powder just falls off the print.” This is especially advantageous since F3DP frequently incorporates honeycomb design in parts to save on material, creating intricate pieces that can be extremely time consuming to post process. “We can clean out parts two to three times faster with ESTANE® 3D TPU M95A,” boasts DeWys. “It’s a huge savings in terms of manpower and the fast turnaround time provides a significant competitive advantage for us.”Superior accuracy and design stability
F3DP is often called upon to create pieces within extremely tight tolerances to deliver a precision fit with other parts. “There’s more stiffness with ESTANE® 3D TPU M95A,” explains DeWys. “This is the only TPU we’ve found that provides the necessary stability to hold its dimensions, so the parts come out exactly how we intended.” This is a key benefit, to say the least. “None of the other attributes mean anything if the part just doesn’t fit,” states DeWys.
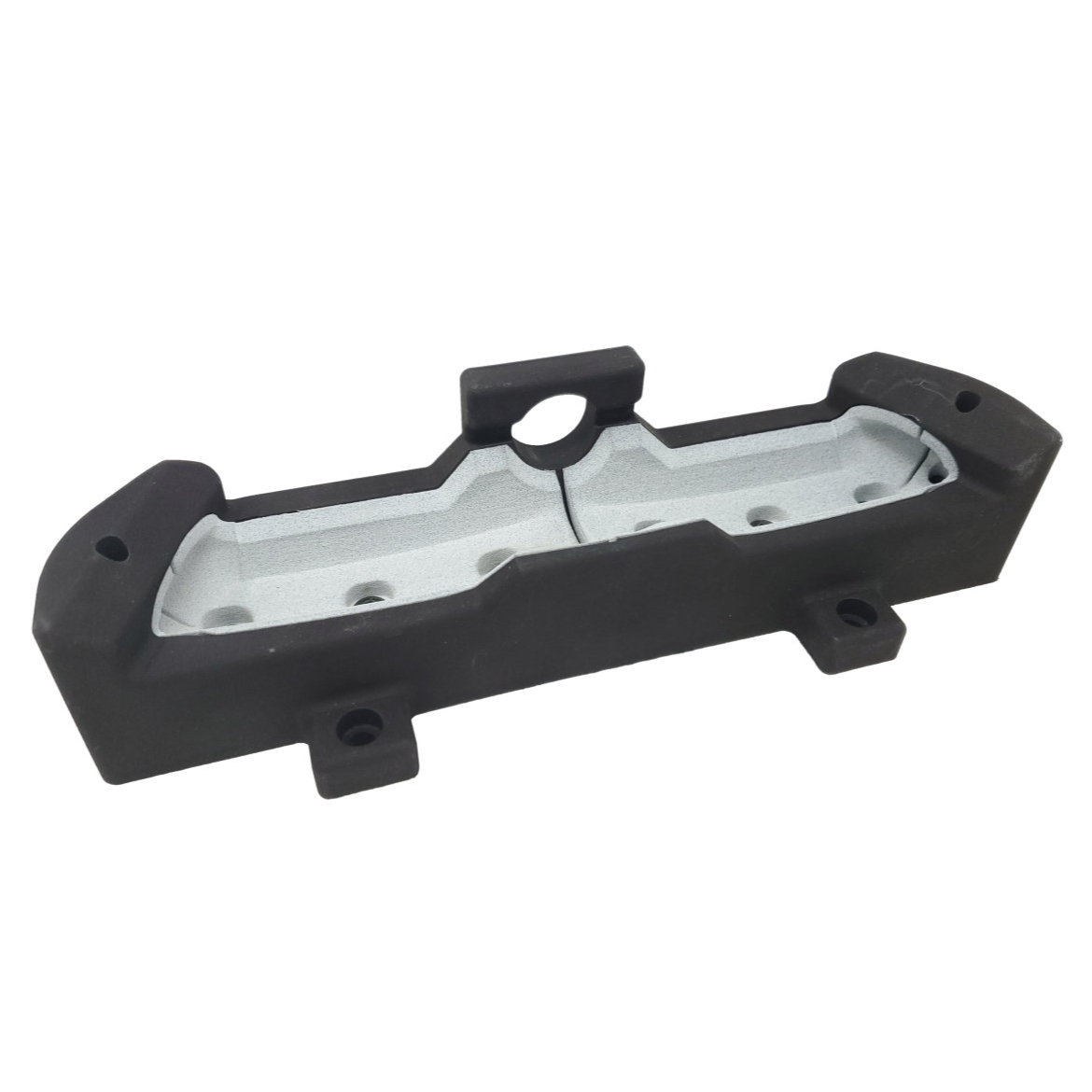
Making an airtight (and fluid-tight) case
The ability to produce soft parts that are both fluid-tight and airtight is another aspect of ESTANE® 3D TPU M95A which F3DP finds invaluable. Creating suction cups is just one example DeWys sites. “Suction cups are commonly used to pick up and handle parts on a production line,” says DeWys. “Having the capability to efficiently custom design and 3D print them to fit virtually any production process is tremendous.” The combination of softness, durability and airtightness makes ESTANE® 3D TPU M95A the ideal material for this application, as well as many others.